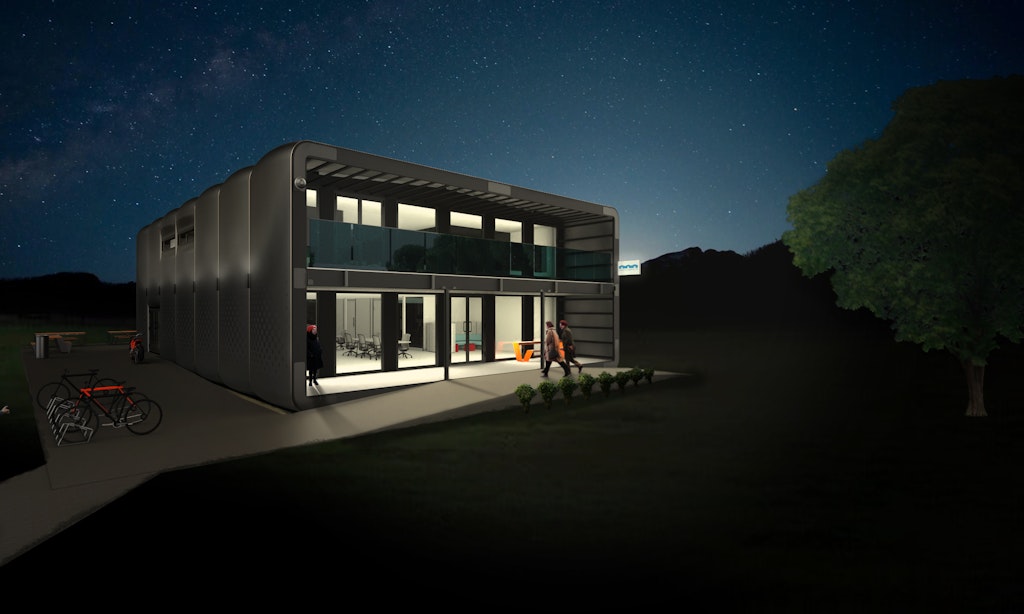
Architectural Solutions. The AirClad Way.
In these strange and uncertain times we are introducing our latest project which also brings a brand new dimension to AirClad systems.
We are excited to have been granted planning permission for our first AirClad office, engineered to accommodate up to 50 members of staff.
The project is now moving into the pre-production phase and, as such, we thought this would be an opportune time to start building a case study around the project.
There are many new developments to the system and our thinking and reasoning behind it.
We will share images and top line information with you at this stage, and build on this as the project takes more shape in the future.
The brief was to provide a new office building for RJL (Richard Johnston Logistics) a rapidly expanding storage and distribution company located on the A12 corridor in Snetterton, Norfolk. This area of the UK is a fast growing business hub, supporting large scale storage and distribution, as it is located near Felixstowe port and strategically positioned for London, the Midlands and North East.
RJL boasts almost one million SQ FT of letting space and has plans, as well as the land to build more.
RJL is a privately owned, family business, which has evolved from a grain storage business in the 1970’s into one which now stores and services many familiar house hold brands.
Our shopping habits are now influencing the direction of development for RJL, and the next 5-10 years will see a growth in automated pick and pack storage and distribution facilities.
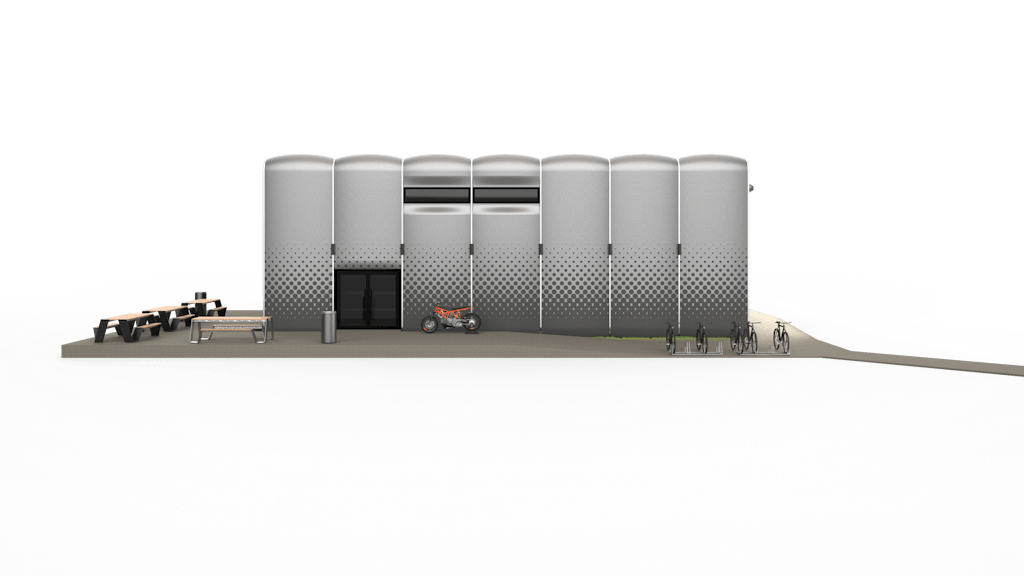

AirClad were initially asked to supply a fast but temporary solution to handle an immediate staff over flow. However, it soon became clear that their plans to build a new purpose built office would be 3-4 years off.
As a result, we, together, made the decision that a ‘quick fix’ solution, would not be on brand nor recognise the importance and commitment RJL has to its’ team.
With the above in mind, we agreed to develop the core AirClad system to be engineered as a permanent building that would meet planning regulations.
Design wise, we challenged ourselves to exceed the needs and exceptions of their team, yet be 100% reusable.
Our philosophy is that we design and treat our buildings as products with a key prerequisite being that everything needs to be designed to come apart and be relocated when it is no longer needed, no matter how long it is used for.
To achieve this, all materials and fixings are of the highest quality, beyond anything used in normal prefabricated buildings and more in line with the marine & sailing industry.
Being able to disassemble a building and reassemble it, or scale it up or down (like a huge Meccano set) has many benefits. Our buildings can be repurposed as well as relocated.
So many derelict, unwanted buildings sit empty.
If we could move those building where they are needed the most, change the use or rescale them, we could go towards preventing the over production and consumption of resource.
Form a design and function point of view, the life span of a building can be extended, there is a compelling argument to support the investment into the best materials and quality fittings.

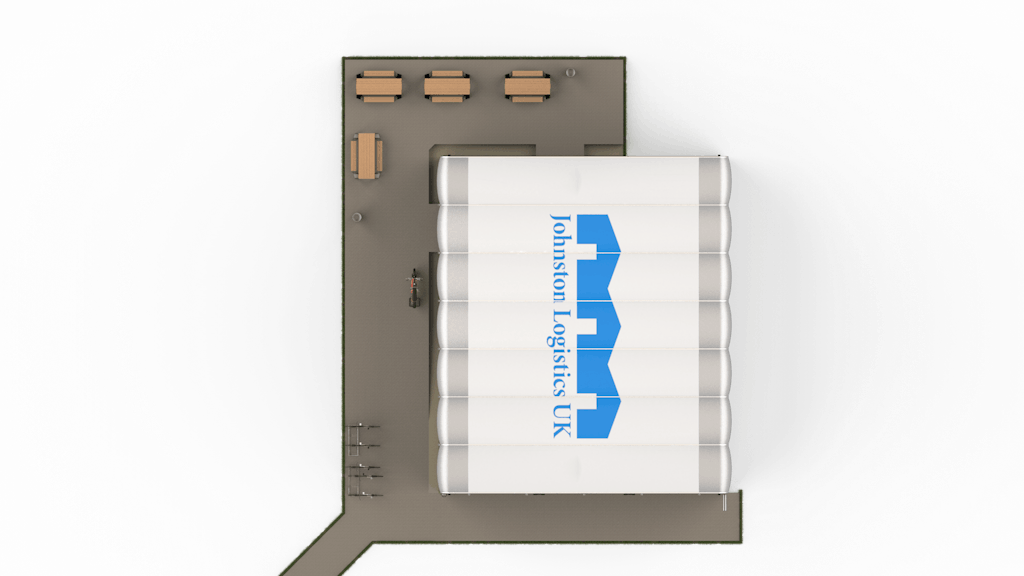
The project discussions commenced in the summer of 2019, and the speed of development has been rapid.
The formal go ahead was given in early November of the same year and work to design the building was run in parallel with both RJL local engineers Plandescil Ltd and our structural engineers in London, Webb Yates.
On one level the brief was relatively simple with an exact time frame in mind, however, the fact that we now have the full planning consent, the time the building remains in situ is no longer a factor.
It is also worth noting that the planners have been surprisingly taken with the AirClad scheme presented.
They commented that their concerns with typical temporary offices, is that people erect cheap shabby cabins that tend to sit there for years, becoming a permanent, accepted blight on the landscape.
They noted that as our solution is engineered to be reused, in combination with the high quality spec,, they had absolutely no issue to grant full planning.
The current RJL office building on the site has been out grown in both scale and by the changing ways we work.
We wanted to develop a design with maximum flexibility to accommodate open plan spaces for the big team and complement this with a series of glazed offices for meetings and staff where privacy is essential.
In addition, we have also allowed space for breakout meetings and a reception.
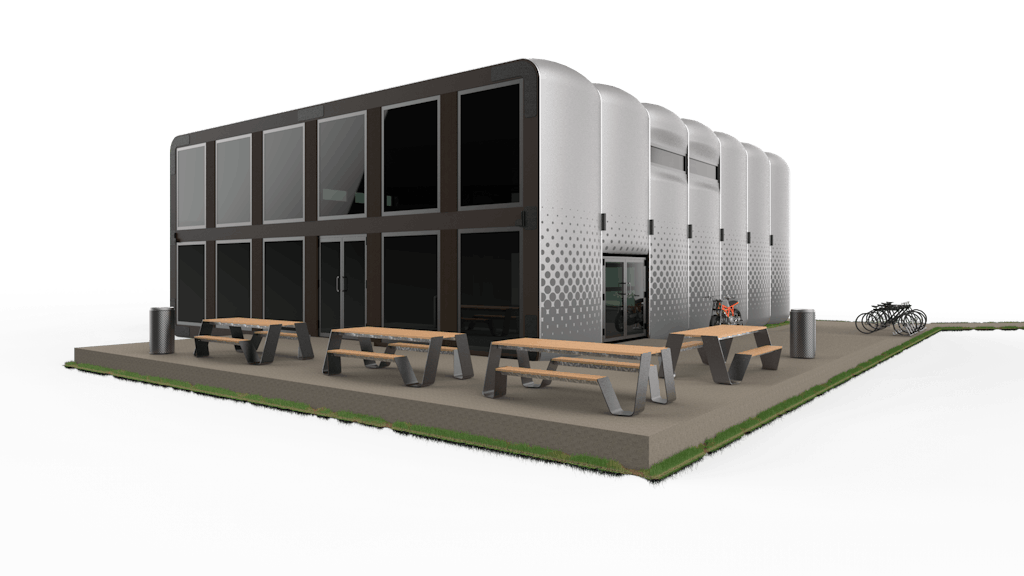
To accommodate all the above we have landed at a two storey space with 225m2 on each level.
The general dimensions and scale of the building have not changed from the outset.
Through the engineering and preplanning phases, we have needed to amend many details to accommodate those specific requirements.
In many ways these have had a more than positive effect on the design process.
The biggest challenge faced was to maximise the glazing and offer all staff the best possible inside out views.
Achieving this and complying to regulation ‘Part L’ has been this biggest challenge of all. Our process differs to a regular architectural project or that of producing a temporary structure.
We have our own unique technology and systems of construction, so we often begin by presenting existing products and projects to explain the functionality.
We then carefully listen to the needs of the client or project.
A process of exploration develops between all parties as we navigate through ideas and opportunities, presenting back concepts and the creative reflections we take out.
Experiencing structures being built in the flesh can be invaluable. Layer this with sketches and rendered visualisations, we can quickly produce the most suitable direction for projects.
Early engagement with our engineers is essential to give them the scope of what we are looking to produce and as they are familiar with our systems they can give informal advise while we stay focused on the requirements of the client.
This in turn helps to avoid any potential issues further down the road, whilst not drowning the client in a load of often daunting, technical data.
We have worked with the engineers, Webb Yates for 15 years.
All of our early engineering concepts and testing was carried out with them that helped push the strength of AirClads to their maximum potential. It is the first time we have worked with Plandescil who have done a huge amount of the heavy lifting with the planning phase.


Most of our learning to date has been around how we balance the need to have a 100% reusable building as well as to comply with building codes.
As this is our first project of this type we prepared to take on many new, unknown challenges.
The commercial viability of the project being one of them, as it is as important as all the other parts. After all, nothing is gained if we end up with a solution that is simply not affordable.
Simplicity is a key attribute to what we do at AirClad and less is definitely more.
How we do less with more is both important for the environment as well as the balance sheet. We want this Office space to be a testament to a great minimal design solution.
Great design is built on time and knowledge and if we dedicate enough time and consistency to it, we will produce better and better solutions.
This is the reason why AirClad exists. We are product designers, and unlike architects we are striving to create the ultimate system to create architectural products.
To achieve this, we must stay focused on the system and not one off-site specific projects as architects do. They start from scratch each time, we have a head start each time based on the knowledge gained that enables us to be better and faster from project to project.
Think of a Porsche 911, ultimately the same car just refined and improved over time. Arguably the best sports car in the world.
This project is currently on track for delivery and installation in May 2020, however, as we write the world is on lock down and for the safety of everyone we work with, it is likely this project will be delayed to then end of Summer/early Autumn all being well.
We are using the lock down time effectively to work on more of the interior fit-out details and to reflect on all the engineering and planning details to build even more details as to how to produce AirClad architectural spaces.
Along side this project, AirClad have been developing home offices, living pods and study rooms. We hope as the world returns to some sort of normality that we can show more of these projects in the flesh. Message us here to find out how we can help.

